Modeling Services
Sunstone Services Group offers a wide range of computer modeling services. Computer modeling plays an increasingly important role in all aspects of today's projects. By using these technologies, we are able to identify potential issues early, streamline workflows, and deliver the project ahead of schedule.
As technology continues to evolve, so do the applications of computer modeling services. From augmented reality integrations to AI-driven analytics, the future holds exciting possibilities. Stay ahead of the curve by keeping an eye on these trends. Let's move into the future together.
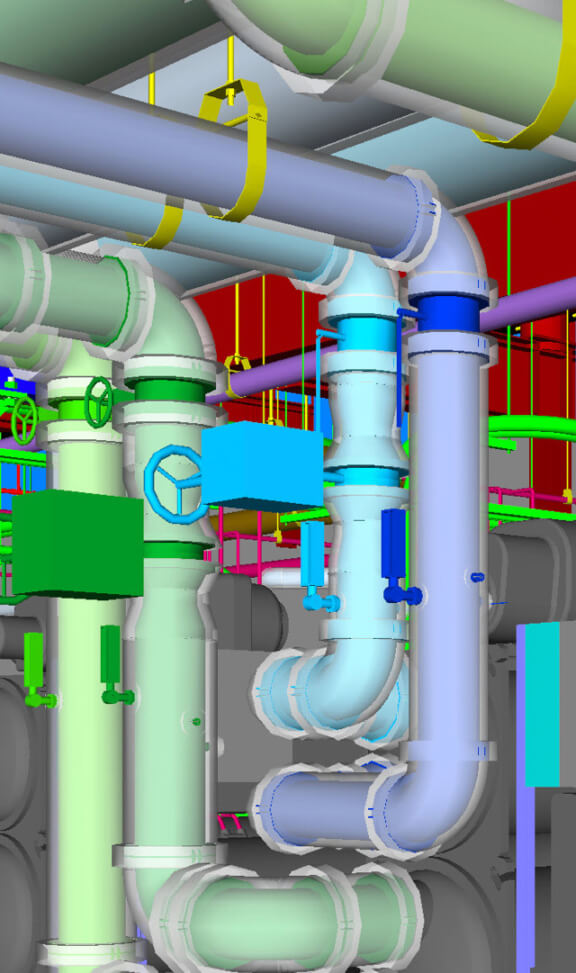
Computational Fluid Dynamics (CFD)
Computational fluid dynamics (CFD) is a technique for modeling fluid behavior. In building design, it's typically used to model the movement and temperature of air within spaces. This is important as it allows designers to investigate internal conditions before a building is built, test options, and select the most effective solutions.
CFD allows designers to identify:
- The thermal comfort of occupants.
- The distribution of environmental conditions within a space.
- The effectiveness of building services (such as the positioning of air inlets and extracts or radiators).
- The consequences of fire (such as the spread of heat and smoke).
- The effectiveness of natural ventilation (such as the stack effect).
- The buildup of heat in specialist spaces such as server rooms.
-
The positioning of sensors.
- For example: the temperature at the top of a tall space might be very different to the bottom.
- This can be important when positioning temperature sensors that feed back to the building management system.
- Otherwise, heating and cooling might be operating unnecessarily.
CFD can also be used to investigate the impact of a new building on air movement around a site and has been used to model other 'fluid' behavior, such as the movement of people. Simulations are typically run for several scenarios, testing behavior under varying levels of occupancy, different climatic conditions, different modes of building services operation, varying openings between spaces, and so on. This can show how a building will likely behave under normal operating conditions and during unusual or extreme conditions.
3D Scans
Utilize the latest 3D laser scanning technology to deliver accurate and detailed information. 3D Scanning Services Include Reality Capture Solutions for the Architecture, Engineering, and Construction Industry.
3D Solution Specialists head out to your job site for data collection using the latest 3D documentation technologies validated by proven dimensional survey control techniques. The acquired data is imported into cutting edge automated feature extraction software that quickly and accurately converts the data into a comprehensive 3D Building Information Model (BIM). You get to save time and money by designing and building around actual “as-is” project conditions instead of relying on out-dated drawings that no longer represent the real world.
3D Scan-to-BIM solutions utilize 3D laser mapping to capture vital as-built facility and systems data that can be imported into software applications. This allows us to translate 3D point clouds into BIM software object families. By making the up-front investment in 3D reality capture before a renovation project, you get the advantage of designing around actual building conditions instead of old drawings that no longer represent the real world facility. Owners find that the overall cost of 3D laser mapping and scanning - and BIM services - is usually far less than the cost associated with a single, major field change resulting from poor and inaccurate as-built data.
Benefits of 3D Laser Scanning over Conventional As-Built Methods
Save Time
- Measure a structure's physical property 10x faster than conventional techniques.
- Create BIMs and CAD drawings directly from point clouds.
- Validate and document design changes using real world, as-built information.
Improve Accuracy
-
Easily measure difficult or hard-to-reach areas (e.g., predesign site conditions, underground utility structures, ceiling enclosed MEP systems, etc.).
-
More accurately capture “as-is” project conditions with BIMs created from point clouds.
-
Measure precisely within 2mm to 5mm depending on distance to measured object.
Save Money
-
High coverage of the scanned area minimizes (if not eliminates) costly return trips.
-
Reduce costs by creating 3D digital reproductions of existing conditions to help detect clashes and minimize expensive field changes.
-
Eliminate re-design work orders due to poor quality as-built record documentation.
-
Improve margins by as much as 10%—either keep the savings or apply it to make proposals more attractive to potential clients.
-
Maximize your technology investments through native compatibility with Autodesk® Revit®, AutoCAD®, Bentley MicroStation® and other mainstream modeling, design, and documentation applications.
Own Your Deliverables
Depending on services selected, you'll keep all your information delivered in one or more of the following ways:
-
Design/Engineering grade 3D point cloud models
-
2D floor plans, sections, and elevations
-
Building information models
-
Clash detection analyses results
-
Project access via Webshare Cloud
Validate Decisions
-
Virtual Project Viewer offers superior project documentation through interactive 360° panoramic point-and-click, measurable images.
-
View and measure scanned data using free software, providing stakeholders the information they need to substantiate crucial decisions.
Create Long-term Value
-
Extract more value from your building information modeling technology investments by incorporating Scan-to-BIM data into your existing BIM workflows.
-
Georeference data to an existing site dimensional survey control.
-
Create permanent, accurate digital records (similar to a digital photograph) that will support buildings throughout their lifecycles.
Industries Served
Architecture & Historical Preservation
Powerful high-definition scanning documentation to support restoration and maintenance.
Our national, state, and local historical buildings, statues, and monuments need to be maintained and often restored. Most are unique architecturally. Therefore, 360 degree imagery and 3D documentation of existing conditions is required before restoration so that there is a permanent record of the building or artifact.
On historical preservation projects, several useful digital survey deliverables can be provided, including:
- 3D point cloud that will serve as an archivable, digital survey record of an existing structure.
- 2D Floor plans, exterior elevations, and sections produced from the point cloud.
- Building information models of historic facilities.
The bottom line is that the 3D point cloud can be used to provide a wide variety of documentation to support the restoration and maintenance of historic structures.
Healthcare 3D Laser Scanning Applications
Utilizing industry standards for 3D laser scanning applications in healthcare facilities.
3D laser scanning applications in the sterile environment of a hospital is a process that requires following strict infection control procedures.
Infection control procedures are usually initiated in hospital areas where patient or operating rooms are located. They are also required in rooms housing assets like sterilization units. The procedures involved enclosing our work space within floor-to-ceiling containment carts prior to removing ceiling tiles to access the plenum and begin scanning. The overall objective is to capture the 3D scans without letting any contaminant from the plenum space or our clothing drop into sterile environments.
Working in a live environment also presents its own set of challenges. Sunstone has project managers who are skillful at working with hospital staff to schedule scanning time windows in ways that minimize disruption.
Industrial & Manufacturing Laser Scanning Solutions
Dynamic 3D laser scanning solutions for dynamic environments.
Industrial and manufacturing facilities are very dynamic spaces and so their laser scanning solutions must be dynamic as well. In industrial and manufacturing facilities, materials and products need to flow through factories with great efficiency to keep costs down and productivity up. That's one of reasons factory owners are forever re-optimizing their floor layouts—moving things around, removing old equipment, adding new equipment, etc. Over time, all these changes can lead to a poor understanding of what is actually on the factory floor, where these assets are located, and how much space they consume in three dimensions.
When scanning a manufacturing facility, the goal is to use laser scanning solutions to create a 3D reality capture of the facility and its contents. Once the point cloud model is turned over to the client, they can bring it into a solution like the Autodesk Factory Design Suite and use it as a backdrop to help place equipment and create new, more highly efficient product flows.
In some cases, a more specific task is required such as scanning the intended path of incoming equipment to its final position. By creating a reality capture, it can help clients accurately calculate 3D space constraints and clearances. We can then model the extents of the new equipment and virtually move it through the path in the point cloud model to find clashes and interferences, minimizing costs and greatly reducing downtime on the line.
3D Laser Scanning for MEP
Accurate measurements—even in crawl spaces and above ceiling tiles.
One of the biggest challenges in an existing building renovation is accurate documentation of the building MEP systems. 3D scanning can be a vital part of this process. If you even have blueprints, it's likely that you'll find that the existing systems were not built as originally designed. And it's not easy getting accurate measurements in crawl spaces or above ceiling tiles.
3D scanning helps MEP engineers overcome these challenges with Scan-to-BIM Services. One advantage of 3D laser scanners is that they can fit into small spaces where people can't go. 3D laser scanning quickly and accurately captures infrastructure located in hard to reach plenum spaces, including visible structural, MEP, and HVAC system elements. Today's advanced point cloud post processing software then allows everyone to “connect the dots” between what the scanner could see and what was hidden to create a complete and accurate engineering MEP as-built point cloud model. In comparatively more open spaces like mechanical rooms, 3D laser scanning is similarly the fastest, most precise method of collecting as-built pipe and equipment information as point clouds that are accurate within 2mm to 5mm.
Automated feature extraction software tools can be used to model elements like pipes and ducts and convert them to BIM object families. When converted to a BIM, the point cloud model allows engineers to quickly access and analyze as-built conditions prior to commencing the design process. If a retrofit has already been designed, we can use the new as-built BIM to conduct 3D clash analyses so problems can be resolved before construction begins, saving both time and money.