Sunstone Services Group commissioning services involve a quality-focused process to ensure that building systems and assemblies are designed, installed, tested, and maintained according to the owner's requirements. This process includes verifying and documenting that all systems function as intended, from initial installation to full operational status. Key benefits of commissioning include improved energy efficiency, compliance with design and legislative standards, and enhanced user experience. By conducting thorough testing and validation, commissioning helps reduce operational risks, maintenance costs, and ensures the long-term reliability and performance of the facility.
Which Projects Require Commissioning?
Commissioning involves replicating various operating conditions to ensure that a system responds appropriately. Any performance issues are recorded, diagnosed, and resolved on-site. Once complete, the system is verified to be in perfect working order.
Commissioning services provide a detailed assessment of your equipment, helping you avoid breakdowns and unproductive workdays. This process ensures that your operations run smoothly and efficiently.
Any critical system should receive regular commissioning. Additionally, commissioning should be performed for any project that involves automatic mechanical controls.
The Commissioning Process
The commissioning process begins with a thorough check of the equipment after it has been installed. This involves verifying that the correct equipment and materials have been installed in the proper location, and that the installation meets construction details and the manufacturer's requirements. A custom checklist and documentation of the installed equipment must be created.
After verifying the correct installation, the next step is to witness the equipment's operation. This includes verifying and documenting proper operation, such as startup, shutdown, and sequence of operation. Any issues with the sequence of operations or startup and shutdown must be reported to the necessary contractors immediately. Once the equipment is verified to operate properly, it can be tested, adjusted, and balanced (TAB).
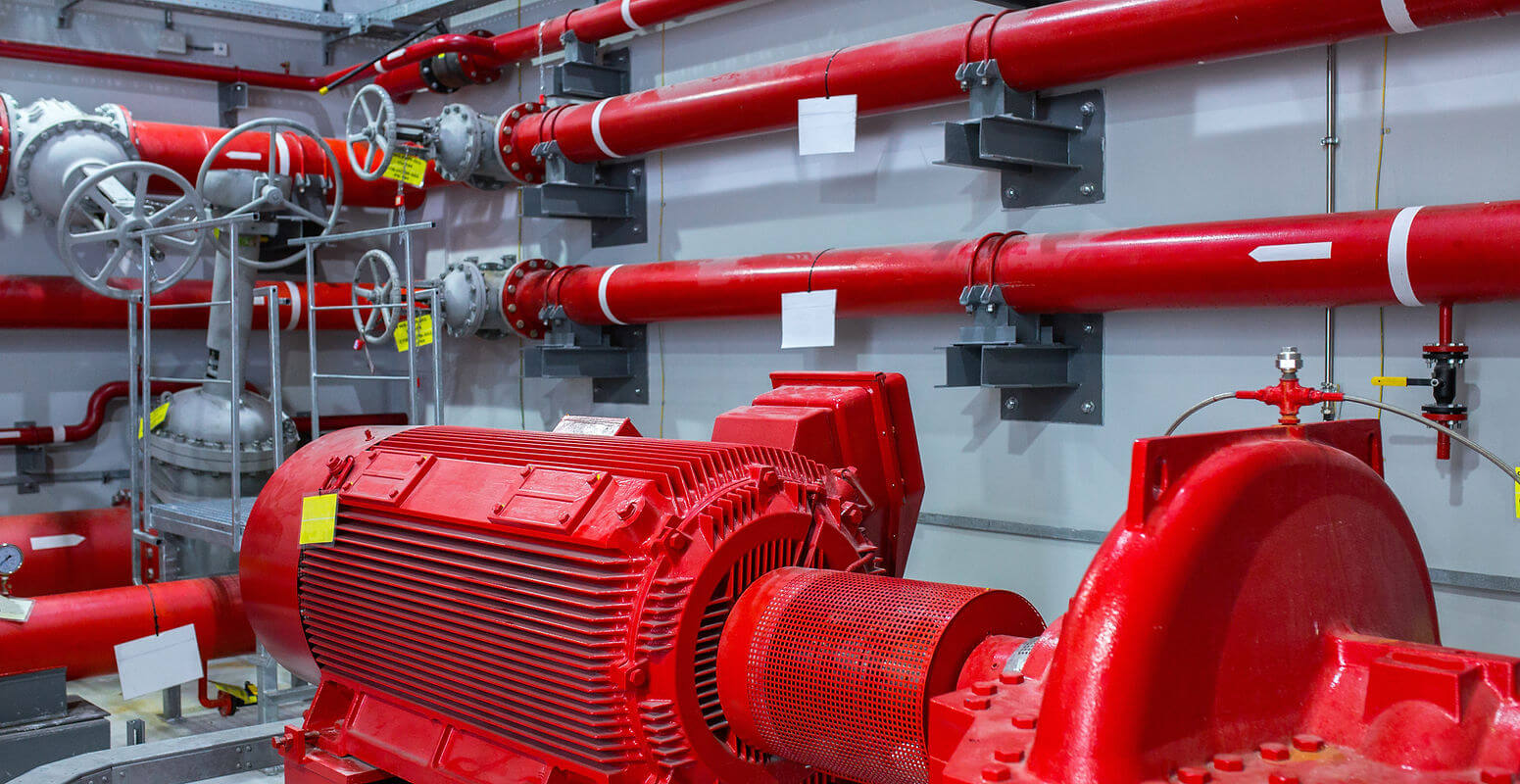
Types of Commissioning
Existing Building
Existing-Building Cx (EBCx): a quality-focused process for attaining the Current Facility Requirements (CFR) of an existing facility and its systems and assemblies being commissioned. The process focuses on planning, investigating, implementing, verifying, and documenting that the facility and/or its systems and assemblies are operated and maintained to meet the CFR, with a program to maintain the enhancements for the remaining life of the facility.
Retro-Commissioning
Retro-commissioning is used on a building which was never commissioned previously.
Retro-commissioning is quite similar procedurally to standard commissioning, while being quite different for the client. Like building commissioning, retro-commissioning takes a broad look at the interactions between the many systems in a building and seeks to optimize them in relation to each other for the best possible interior conditions. What can be very different for the client is the price: retro-commissioning is performed on buildings with systems that have already been constructed, and oftentimes very cheap and simple tweaks can produce incredible leaps in efficiency.
"The kinds of problems that retro-commissioning will identify and fix include: equipment or lighting that is on when it may not need to be air balancing systems that are less than optimal…[and] controls sequences that are functioning incorrectly.”
From this description, we can begin to see why many of these changes can be surprisingly cheap. Reprogramming controls sequences does take a skilled technician, but it also doesn't require the purchase of replacement parts or the redesign of entire systems, which can get expensive quickly.
How can you know if your building would be a good candidate for retro-commissioning? Well, a good first indicator is that something has changed lately. Perhaps your energy bill is steadily rising, and user behaviors have been ruled out, so you suspect it's your building itself that is no longer performing as intended. Or perhaps your building has recently undergone a use shift, such as a re-zoning from industrial to commercial. Perhaps your building is now home to more users than it was originally designed for. In times of change such as this, it can be difficult to shift the focus back to the underlying systems that often feel invisible when functioning correctly. However, a well-timed building retro-commissioning can open the door to recurring savings that really start to add up. Much like energy auditing, retro-commissioning is cost-aware.
The deliverable is often a ranked list of proposed modifications, ranging from least to most cost effective. While ideally a client could make all suggested adjustments simultaneously and reap the maximum cost savings, the reality of business finance makes it a wiser choice to prioritize. This allows the client to perform their own cost-benefit analyses based on liquid capital versus desired recurring savings and environmental benefits.
One of the largest barriers to successful retro-commissioning is persistence. Accidents like software resetting or the continual user override of control systems can have a deleterious effect on the energy savings that this service provides. This is the flip-side to the fact that many of the upgrades can be small, cost-effective parameter tweaks; the parameters can be reset again poorly if persistence is not highlighted. Ways to increase the persistence of the retro-commission benefits include employee briefings and clear signage. If the building administrator is committed to sustaining these changes because of the cost savings they provide, retro-commissioning can be a secret weapon in the fight against monthly cost bloat. If increasing your building's performance can be as simple as a few adjustments, why not give it a try?
Re-Commissioning
Re-commissioning is for a building which was commissioned previously.
evaluate and test an existing building's systems to determine if they are performing as intended. In typical building operations the "wear and tear” on systems can cause them to operate inefficiently or malfunction all together. improve a building's operations and maintenance (O&M) procedures to enhance overall building performance. These improvements often result in lower building operating costs and a reduction in energy waste.
Re-commissioning, which evaluates and tweaks the systems of an existing building, is a similar process. Evaluating HVAC system designs is a large part of building commissioning, as defined in ASHRAE Guideline 1.1-20071.
Re-Commissioning is an application of the commissioning process requirements to a project that has been delivered using the commissioning process. This may be a scheduled recommissioning developed as part of an ongoing commissioning process, or it may be triggered by use change, operations problems, or other needs.
LEED Commissioning
LEED Commissioning requires developing a commissioning plan for testing energy-consuming and environmentally related systems, plus their equipment components. Commissioning is a prerequisite for almost every LEED rating system. Having completed over 200 LEED Commissioning projects, including 19 Platinum projects, Sunstone has performed existing, fundamental, and enhanced commissioning for LEED-NC, LEED-EB, LEED-CS, LEED-CI, and LEED-S projects. Suntones's independent commissioning group is a team of professionals capable of providing LEED Commissioning for projects with other design professionals.
A client is seeking to construct a building that will be marked as environmentally friendly through LEED certification. "The commissioning process must begin early in the design phase of a project for owners seeking LEED certification of their facility. For non-LEED certified buildings, the commissioning process can be limited to the construction phase only.”
This is due to the high standards that a building must meet in order to attain any of the LEED certification levels; things as rudimentary as the positioning of a building in relation to the region's solar trajectory patterns can affect both the basic architectural design and the parameters for the HVAC system installed therein.
New Building
When a building is initially commissioned it undergoes an intensive quality assurance process that begins during design and continues through construction, occupancy, and operations. Commissioning ensures that the new building operates initially as the owner intended and that building staff are prepared to operate and maintain its systems and equipment.
initial commissioning, occurs during the production of a new building or on a new HVAC system within an existing building. This is an integrated, systematic process to ensure, through documented verification, that all building systems perform interactively according to the "Design Intent". The commissioning process establishes and documents the "Owner's Project Requirements (OPR)" criteria for system function, performance expectations, maintainability; verify and document compliance with these criteria throughout all phases of the project (design, manufacturing, installation, construction, startup, testing, and operations). Commissioning procedures require a collaborative team effort and 'should' begin during the pre-design or planning phase of the project, continue through the design and construction phases, initial occupancy phase, training of operations and maintenance (O&M) staff, and into occupancy (for warranty and future re-commissioning).
Historically, “commissioning” as referenced in building design and construction, referred to the process by which the heating, ventilation, and air conditioning (HVAC) systems of a building were tested and balanced according to established standards prior to the Owner's acceptance. HVAC commissioning,historically, didn't include other, interactive, supporting, or supplemental building systems that did not directly affect the performance of the HVAC systems.
In 2005, the U.S. General Services Administration (GSA) published The Building Commissioning Guide. The guide provides a process for including building commissioning in the planning, design, construction and post-construction phases of a project. Through energy and water conservation, occupant comfort, life-safety, systems criticality, and technology improvements of building systems became more in demand, and expanded the Owner's performance and technical capability expectation. The need to improve, integrate, and commission other (and more) systems expanded the scope of Building Commissioning. In modern facilities, buildings, and systems many of the systems are integrated (directly or indirectly) in operation, affect, need for proper operation, function, control, and sequencing. This can become very complex, and provide many points of sub-optimal operation, or failure, with all the many systems requiring, or affecting, interaction of each other.
For example, power sources (utility, generation, battery/cell) control and monitoring, air movement control, smoke control, fire suppression, fire alarm, security door egress/evacuation control, elevator control, space containment/infiltration, staging and sequencing of every interacting system, its sub-system, equipment, and components each operating and interacting correctly in every operating Mode (normal, startup, shutdown, maintenance, economy, emergency, etc.).
This list can go well beyond this example, even in the most basic, typical, facility today. As more building systems are integrated, a deficiency in one component can result in sub-optimal operation and performance among other components and systems. Through system testing and "integrated systems testing" (IST) verification of all interrelationships, effects, modes of operation, and performance can be verified and documented to comply with the 'Owner's Project Requirements' and Architect/Engineers documented 'Design Intent' performance.
Thus, 'Whole Building Commissioning' (or 'Total Building Commissioning') is the accepted normal/standard, certainly for government and critical facility Owners, but also for conservation and efficiencies to provide a fully verified operational facility. Partial building commissioning (commissioning only specific equipment, functions, systems) is also still utilized, but the interrelations of many automated systems, as designed, today branch and spider throughout many other systems within even basic buildings.
The new construction commissioning process includes multiple activities performed in a specific sequence. As defined in ASHRAE Standard 202-2018, Commissioning Process for Buildings and Systems, these functions are required to provide a complete commissioning project.
- Initiation:
- Owner's Project Requirements:
- Commissioning Plan:
- Basis of Design:
- Specifications:
- Design Review:
- Submittal Review:
- System Verification:
- Functional Performance Testing (FPT):
- Issues and Resolution Log: participants that need solutions to facilitate successful project completion
- Systems Manual:
- Training:
- Seasonal or Deferred Testing:
- Commissioning Report:
CX Organizations
APPA - Leadership in Educational Facilities (formerly Association of Physical Plant Administrators)
ASHRAE - American Society of Heating, Refrigeration and Air-Conditioning Engineers
ASTM - American Society for Testing Materials
BCxA - Building Commissioning Association
CIBSE - Chartered Institution of Building Services Engineers
EERE - U.S. Department of Energy Better Buildings Initiative
Energy Systems Laboratory - Texas A&M University Continuous Commissioning®
IES - Illuminating Engineering Society
NEBB - National Environmental Balancing Bureau
NFPA - National Fire Protection Association
SMACNA - Sheet Metal and Air Conditioning Contractors National Association
USGBC - U.S. Green Building Council